As Summer drew to a close and the sun began to set earlier, we found ourselves returning home from cruises in the dark more and more often. Ol' Rusty's stock headlights do the job but leave a lot to be desired compared to their modern counterparts. I started researching modern headlights until out of the blue, I received a marketing email from NPD declaring, "Halo LED Lights from NPD!". I raised an eyebrow and opened the email and read on,
"Based around a Xenon H4 style center bulb, the perimeter features 21 super bright LED bulbs. Two versions of the bulb are available: standard white LEDs or a multi-color that features up to 16 different options. Either way, the Halo LED bulbs have an average life span of 100,000 hours, meaning this could be the last set of bulbs your classic needs!"
Hmmm... I was intrigued by the claims and the thought of the halo LED ring had my attention. I clicked on the link in the ad which took me to the
NPD web page for the lights. The price took me aback and I felt that there was no way on this green Earth that my wife would even remotely consider it but there was nothing to be lost by showing it to her so I did and to my surprise, and her credit, she liked them! I then recalled that it was originally her idea to do the sequential tail light upgrade as well. Hmm... the wife likes BLING!
I'm not one to just go out and plunk down hundreds of dollars on something like this without mulling it over... a LOT. A couple of weeks went by before I decided that, A) this might be something I would like to do and B) I didn't need the fancy-schmancy
multi-color LED option; white would be sufficient. So I went back to the NPD web site to order them and... damn... sold out. I emailed NPD's customer service and asked them to email me when they received more. A couple of weeks later, I got an email from "Darrin" indicating that they had more in stock. I placed the order and waited and a few days later I got a box containing two headlights and some wiring harness extensions.
Apparently, the LED "halo" ring could either be illuminated on the same power line as the headlight "dim" signal or from the parking light signal. I decided that although the wiring would be slightly more complicated, I would like the LED rings to light up when I pull the headlight switch out to the parking setting and remain illuminated with the headlights. The headlights contained the normal three-pole connector as well as extra 12 volt + and - leads with no kind of connector. Now, LEDs don't require much in the way of current (electrical, not oceanic), so the type of connector really doesn't have to be as robust as a regular 12 volt light bulb power source as for head, tail, or parking lights or similar but they would still have to withstand weather and driving conditions. The connector would only be the first problem, the second would be where and how to tap the parking light(s) power lines? If I had any patience whatsoever, I would have ordered something like
THIS or even
THIS (cut in half to make one set). But I didn't have the patience. What I had instead was a set of Molex dual-contact connectors that I had used for other electrical projects. They weren't really moisture proof but I had a plan for that.
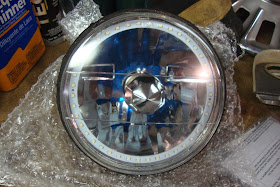 |
Xenon H4 with and LED halo around the perimeter. |
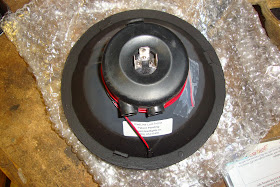 |
The back side. Standard 3 prong connector and a 12V LED power lead. |
I unwrapped the 12V LED leads from around the headlight, wrapped them together with electrical tape, and crimped and soldered the male poles to their ends. Male poles are generally used for negative (ground) lines or terminated lines that don't have a power source. The concept is that if they accidentally come into contact with a grounded surface, they won't short out. They were then inserted into the female Molex housing and protected with heat-shrink tubing.
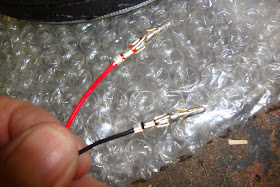 |
Male poles soldered to the LED leads. |
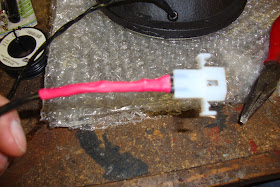 |
Molex connector for the LED power supply |
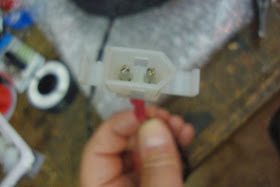 |
The business end of the LED power connector |
The headlights also came with new, ceramic, headlight power harnesses that were designed to isolate the factory harness from the head of the H4 bulb. These were simply pressed onto the 3 bulb leads.
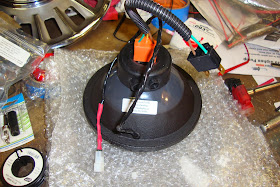 |
Assembled and ready for installation |
A pair of short leads were then prepared with the female poles inserted into the male Molex housing. This "pigtail" would be the power supply side that would be soldered to the parking light leads. They were assembled such that even if the connector came apart from the headlight lead, there was no chance of shorting against the grounded vehicle frame. If I had used the vintage automotive style connector with one pole exposed, that exposed pole would be the ground lead for the same reason. Safety first.
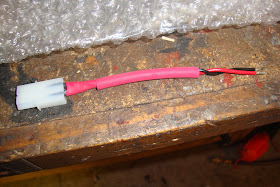 |
The parking light power pigtail. |
After the headlights were prepared for installation, the old headlights were removed from the car. 3 screws to remove the beauty ring and three screws to release the bezel from the housing and the old bulbs could be removed and unplugged from the factory harness. The car was jacked up and the wheel removed to allow access to the underside of the fender.
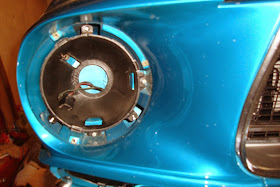 |
Ready to accept the new headlight |
The new headlights came with little square foam pads that the instructions suggested I should stick to the inside edge of the bezel to protect the lenses against cracking. I complied.
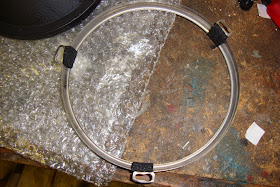 |
The recommended bezel pads to prevent breakage. |
The new headlights were then placed inside the original stainless bezels. The foam pads helped hold them together but also prevented the headlights from being freely adjusted within the bezels while on the car. This required that the bezels be pre-aligned with the headlights before installation. I found that the best position was with the "P" in "TOP" (embossed on the tops of the lenses) be aligned with the leftmost end of the adjustment slot in the bezel. The pic below is slightly off and would result in the light being slightly crooked in the headlight bucket. After I had discovered this, I had to remove the headlight again, and adjust the bezel to the alignment previously suggested above. The headlights were then inserted into the housings in the buckets, fishing the harnesses down into the holes in the back of the housings so that they could be accessed from the wheel-well side of the fender.
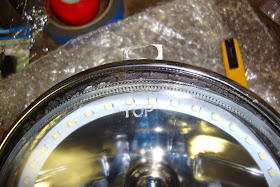 |
Bezel aligned (poorly) to the headlight. Put the "P" under the left end of the slot. |
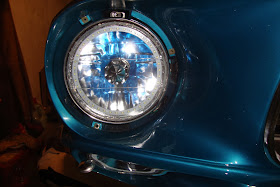 |
Headlight installed but missing beauty ring. |
I think that the ultimate perfect method to complete the actual wiring of the power supply pigtail for the parking-light-to-LED-Halo would have simply been to make a "Y" connector that split power off from the parking light's connector off to he LEDs. Instead, I made the task more difficult than it had to be by splicing directly into the parking light's lead. This was accomplished by stripping the covering off of the lead and then stripping the insulation on the outside edge of the ground and signal leads and soldering the black (ground) lead of the pigtail to the black wire and the red (+12V) lead of the pigtail to the brown wire. The soldered splices were then individually wrapped in electrical tape and then collectively wrapped. I would have preferred to use shrink tubing here but couldn't think of a method beyond simply cutting the wires and building new junctions.
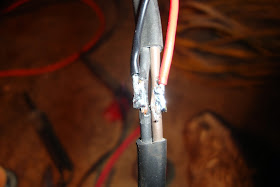 |
Soldered LED splice to the parking light lead. |
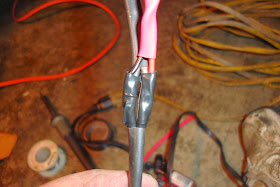 |
Taped up. |
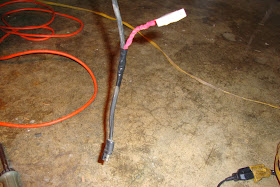 |
Ready to go. |
The pigtail was finally mated with the LED power lead and the whole connector assembly was wrapped in
silicon tape to defend it against moisture, dirt, and rocks.
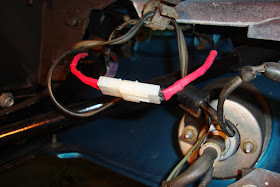 |
LED power lead connected |
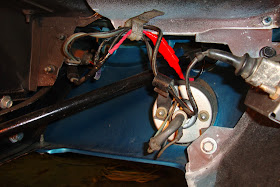 |
Wrapped in silicon self-fusing tape. |
The moment of truth was upon me. I nervously connected the battery cable, walked around to the driver's side window, reached in and pulled the switch and... It's ALIVE!
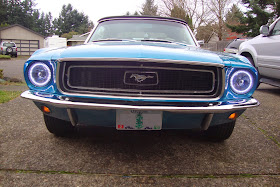 |
Parking lights |
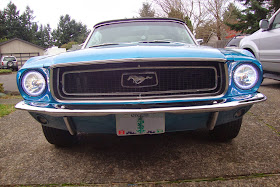 |
Headlights. |
Pretty darned-tootin' cool if I must say so myself. The multi-color version comes with a remote control and a computer that needs to be wired in as well and allows you to adjust the LED colors to suit your mood. As tempting as that is, I think I'm good with the way good-ol-fashioned white looks.
I re-aligned the headlights using the factory service manual as a guide and went for a night drive, on purpose this time, and sure-enough, they work as headlights too. I'm happy to say that Ol' Rusty's future is looking brighter.
Update (11/25/2013): I
posted on the VMF and got a very negative response. So, if you care what people think about your car or are trying to stay stock, don't do it! :-)