I was getting pretty far into the build and remembered that I hadn't done a blog entry in awhile so I thought I'd catch up a bit. I may break this into several pages at a later time.
The rebuild and install of the
heater box wasn't just the completion of the under-dash but also the beginning of the completion of the engine compartment because it meant that the remaining holes in the firewall were now filled. Now, the next step seems pretty straight forward but I procrastinated it for a couple of days until I could come to terms with what had to happen next. All the firewall penetration points needed to be sealed and the firewall in general, needed to be
uglified because that's how the factory did it. If the factory jumped off a cliff would I? Probably, but with much introspection first. The problem was that, in my eyes, my firewall was a thing of beauty. Ten times the glory of Helen of Troy, 30 times the beguile of Cleopatra, and 50 times the charm of
Laura Kaeppeler. So, understandably, I cried a little when I smeared a tube of sealer all over every nut, bolt, and rubber plug on my once-pristine firewall. As if that weren't enough of a crime, I followed up with shots of 3M rubberized undercoating. I should be jailed for this travesty.
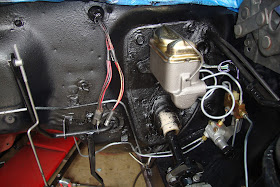 |
Oh man, I think I'm going to be sick... |
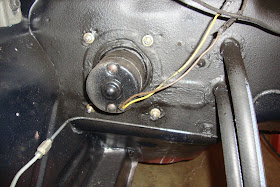 |
Nooooo! |
Also, I installed the ash tray and glove box. No radio yet because I want to weigh my options a bit more. The steering wheel was installed and wired in.
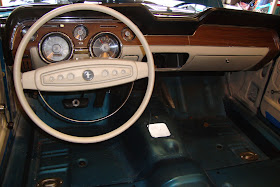 |
Looks almost like it's ready to drive. |
My attention could be turned back to the engine. I installed the backing plate and the flex plate. The transmission linkages and mounting brackets were installed and I poured two quarts of Dextron III. Yes, I'm using Dextron in this C4 (kids, don't try this at home). Fact is that C4's traditionally use "F" type fluid. This serves two purposes. The first is that it didn't attack the old-fashioned organic friction surfaces and seals like the other leading brands but I've replaced all of the clutches, bands, and seals in this C4 with modern materials. Secondly, "F" fluids have less "friction modifier" than Dextron thus provides a better grip to the old fashioned friction surfaces. Too much slip in an old C4 with organic clutches will burn them up. I'm not worried about that for these new clutches. The friction modifiers in DIII may cause the shifting to become "looser" but I'm not convinced that's a bad thing yet. If shifting proves too sloppy, I'll replace it with "F". Some racers use a 50/50 mix of "F" with Dextron to provide a good balance between viscosity and friction with no ill-effects to the trans.
Aaaanyhoo, I poured 2 quarts into the new (purple?) torque converter (TC) and carefully seated it on the input shaft of the C4 making sure to wiggle it and adjust it until it was fully seated on the input shaft, the pump stator, and the TC hub to pump. Regarding how much fluid to place in the TC, my research revealed that the TC could technically be left empty because the C4 pump will fill it within seconds. I also, found more conservative info stating that the TC should contain a couple of quarts so the internal vanes don't spin dry. I went with the conservative method.
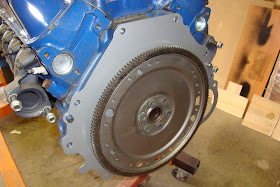 |
Engine plate and flex plate. |
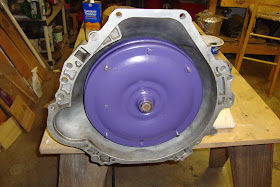 |
Barney The Purple Torque Converter (I spin you, you spin me...) |
Next the engine was mated to the TC. This is a tricky bit but I learned some tricks that worked very well for me. Firstly, the TC is spun to align one of the drain plugs at the bottom of the bell (see above). Secondly, the flex plate on the engine is rotated to align one of the drain plug holes at the bottom of the engine. You can use a short length of tubing over the bottom drain plug screw to help when you align the TC to the flex plate but it wasn't necessary for me. Also, you can temporarily screw a stud into one of the engine trans bolt holes to help align the bell to the engine block. This was another thing I didn't need to do. What I did need to do was to place the C4 on the edge of a table while I lifted the engine with an engine hoist and load leveler and butted it up to the transmission making fine adjustments in position as needed. I think I was channeling old Henry himself from what I've read of others bad experiences with mounting engine to C4 but for me this was literally a non-event. The two practically jumped into each others arms like two star-crossed lovers. It was like, *wiggle* *wiggle* *thunk!* and it was done. I inserted the bolts and finger-tightened them until they were all seated and the gap was closed. No force required.
Once the bolts were in, I torqued them to spec and then rotated the flex plate to access each of the four TC studs and tightened them in turn. The engine/trans was placed on a tripod of three jack stands. One under each motor mount and one under the C4 extension housing where I installed the starter and stored the assembly for a few days until ready to drop it into the car.
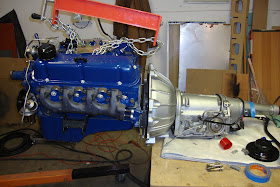 |
Aligning the engine to C4 |
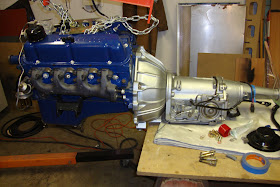 |
The Eagle has landed |
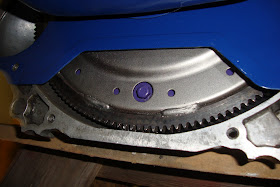 |
The alignment of the lower drain plug with the flex plate drain plug hole. |
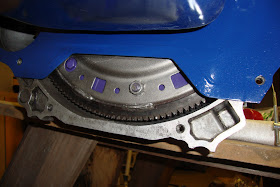 |
Flex plate rotated to install the TC nuts |
A few days after mating the engine to the C4, I was ready to commit to the installation of the engine into it's home for the next 40 years. I backed the car out of the garage to leave myself enough headroom to lift as high as I need to. My garage is weird and has some beams hanging low across the ceiling due to my garage being under living space of the house. Also, it's recommended by many that the back end of the car be lifted to aide in the alignment of the transmission into the tunnel. However, I couldn't do that because of the way my driveway is built. I felt it unsafe to lift the back of the car given the screwy terrain. Fortunately, I had a load leveler but I decided to experiment in its use with a carb lift plate that bolts to the carburetor mounting holes. It did work but the leveler had to be adjusted all the way from end to end to get enough angle on the engine given the short distance between the front and rear mounting points.
Regardless of the issues, my helper (thanks sweety!!!!) held the C4 extension in line with the tunnel while I pumped the hoist and cranked the leveler. After about an hour, we managed to get it down into the engine compartment and aligned with the engine mounts. Some fine adjustments allowed the two mounting bolts into place. The rear of the C4 was supported by a rolling floor jack during the final few minutes to level the engine up and support it while the transmission cross member was installed.
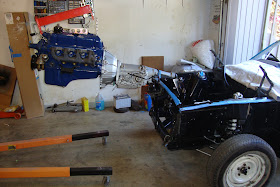 |
Starting the drop |
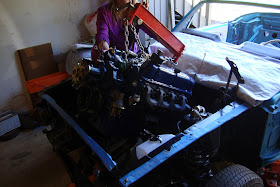 |
Getting there (thanks helper! |
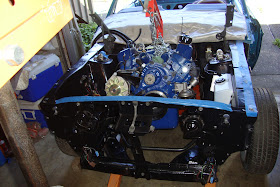 |
Alllllmmmooooossstttt there |
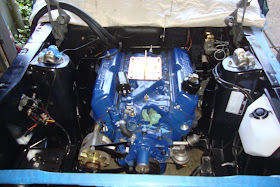 |
It's IN! |
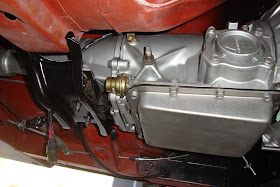 |
Transmission cross member. |
I next hooked up controls that I could such as the trans to throttle kick-down, the speedometer cable, the vacuum modulator line, the fuel line to pump, heater hoses, coil, battery cables, engine gauge harness, neutral safety switch, and the pump cooling fan and pulley. Additionally, the distributor was installed but first, the engine had to be reset to TDC on the compression stroke. I confirmed this by removing the passenger valve cover and confirming that no valves are open on #1 and the timing mark was to zero. The distributor was then marked where the rotor would point to the #1 contact and inserted into the engine block at the point where the gears aligned the rotor to the previously marked #1 position. The most difficult part was seating the pump shaft into the bottom of the dizzy.
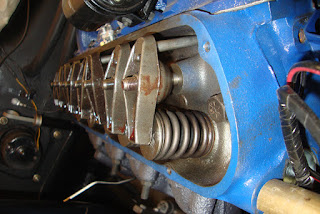 |
Confirming the compression stroke on cylinder 1. |
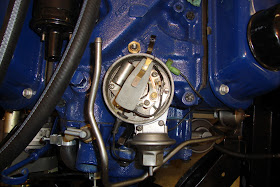 |
Dizzy aligned. |
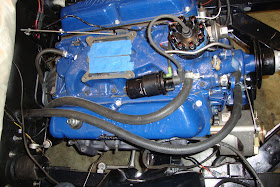 |
Heater hoses and coil hooked up. |
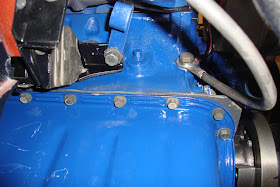 |
Battery ground and alternator ground cables. |
 |
Battery tray with positive battery cable. |
The next little project was the installation of the export braces. A lot of people have trouble with this as the shock towers tend to settle after years and the weight of the engine forces them together a little. All I had to do to get them on was to mount the shock tower ends first and then jack the engine up at the transmission to engine joint to take the weight off the suspension and engine mounts. This was enough to get the bolts into the cowl holes and tighten them up.
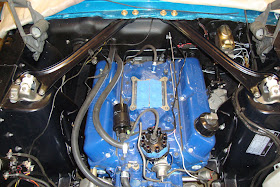 |
The export braces installed between the cowl and shock towers. |
I then R&R'd the shifter housing via the media blast/paint routine. I had some spare parts that I'd picked up at swap meets such as a shaft and handle that weren't pitted. I also installed new bushings as mine were completely gone. After getting the shifter release button working smoothly, I installed it in the car with a gasket between the tunnel and the shifter housing. I set the C4 to reverse (the indent immediately after park) and set the shifter to reverse and tightened the shifter linkage nut. The shifter seems to work smoothly and accurately.
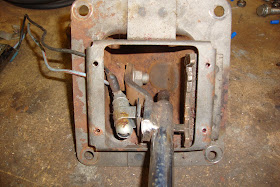 |
A rusty, pitted, shiftless mess |
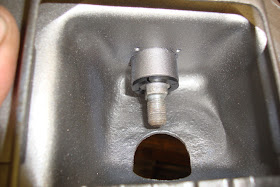 |
Cleaned up, painted, new bushings. |
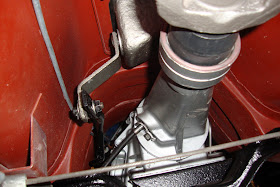 |
Linkage hooked up. |
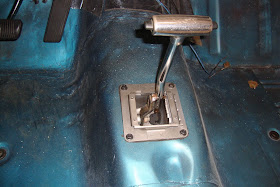 |
Good to go. |
I went so far as to remove the radiator from the shed and clean it up. I did a simple pressure test using a garden hose and found a leak. The radiator has since been dropped off at a radiator shop. Also, a windshield, gasket, and sealer are on order so stay tuned!